Improve Performance & Avoid Down Time
John Deere Connected Support™
CONNECTED SUPPORT
Embrace the power of prediction. Connected Support is specifically designed to give you control of your fleet and eyes on what’s coming. It uses data from thousands of connected machines to help you work smarter. Helping you tackle issues head-on – before they have a chance to slow you down.
OPERATIONS CENTER
Every day, you push yourself to the max — making progress and meeting deadlines. John Deere Operation Center helps you keep a close eye on every detail, allowing you to analyze machine data, track utilization, review diagnostic alerts, and more. That means reduced downtime and elevated efficiency.
MACHINE MONITORING
Being successful means being efficient. Staying on top of machine performance can make that happen. Machine monitoring uses the latest connectivity and alert-management tools to filter and analyze machine data, allowing you to identify critical issues and take action — sometimes before you even know there is a problem.
DEERE MACHINE HEALTH MONITORING
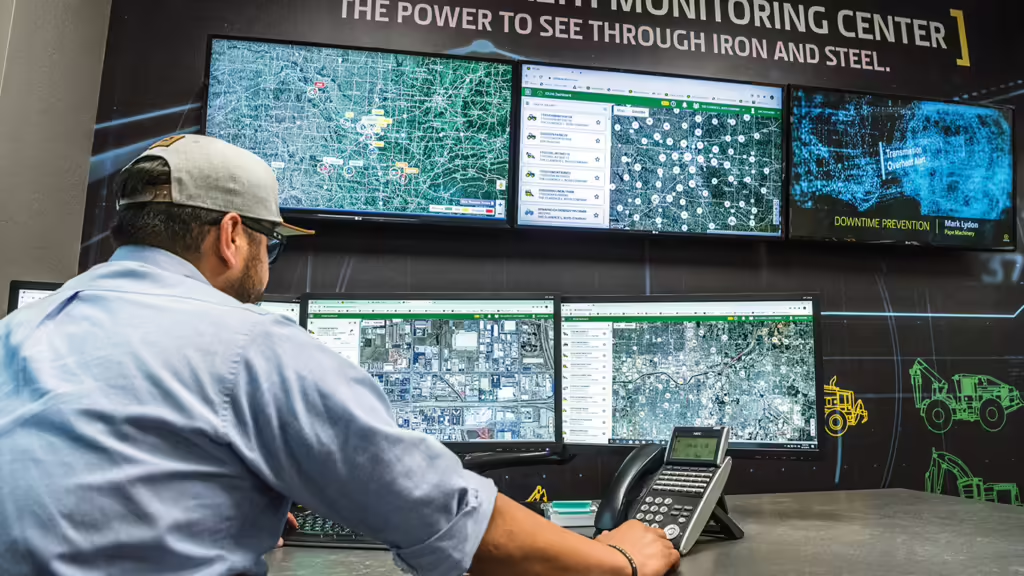
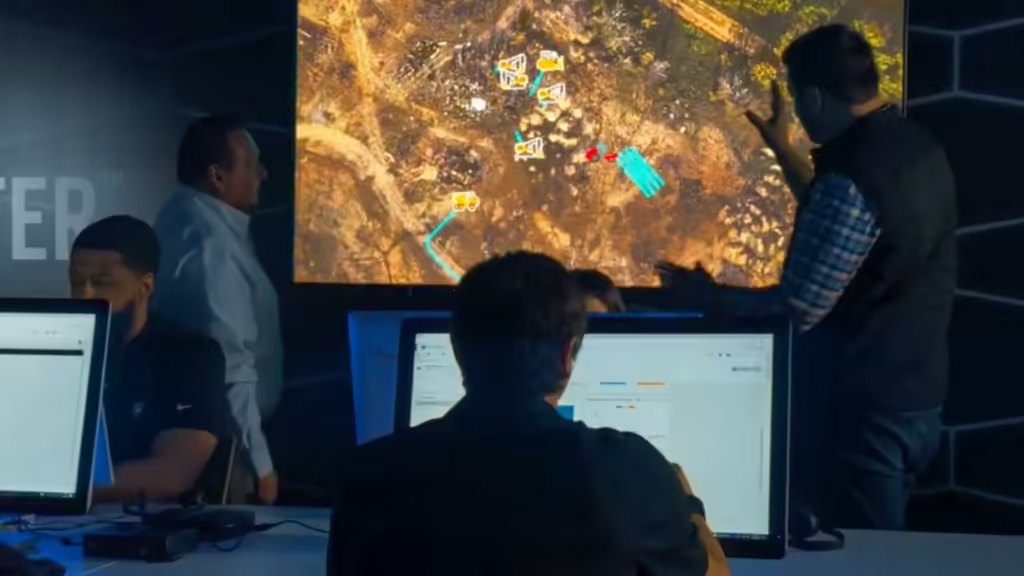
It all starts at the John Deere Machine Health Monitoring Center, which analyzes data from thousands of connected machines. Experts there identify trends, determine what causes common issues, and create new protocols for preventative maintenance and repair.
DEALER MACHINE MONITORING
Your trusted dealer puts the right plan for you into action, delivering solutions with speed and accuracy. Providing the necessary fixes to keep your machines running and your operation humming.
EXPERT ALERTS
Unlock the power of Expert Alerts and protect your bottom line. Expert Alerts is a proactive monitoring system that allows your dealer to keep eyes on your fleet – so you can focus on the job. When you choose to enable Expert Alerts, your dealer can proactively analyze telematics data to uncover potential component failures before they disrupt your operations. With this advanced notification, technicians can make repairs at a convenient time – with minimal disruption to your operation.
Real-World Example How Expert Alerts Saves Dollars:

A customer cutting grade with an 850K Crawler Dozer didn’t have any indication of an equipment issue.
The dealer contacted the customer and received permission to dispatch a technician to replace the pressure-regulating valve.


However, the customer’s John Deere dealer remotely received an Expert Alert indicating low engine-oil pressure for that machine, but not at a level low enough to trigger a diagnostic trouble code (DTC).
REMOTE DIAGNOSTICS
You have dirt to move and we get it – time is money. Lucky for you, you’ve got a team of experts on the lookout who are focused on saving you both. With Remote Diagnostics from John Deere Connected Support, your dealer can troubleshoot machine issues from a distance. Sometimes even solving issues without a site visit. We call that a win-win.

In this industry, uptime isn’t everything – it’s the only thing.
That’s why we pioneered Remote Diagnostics and programming technology years ago – setting standards and driving innovation in our field.
With Remote Diagnostics, your dealer can read and reset trouble codes, record performance readings, and update software without a trip to the site – all so you can keep downtime in the dirt.
Parts for All Equipment
When it comes to keeping your machines running at peak performance, having the right parts is essential. That’s why we pride ourselves in offering a wide selection of top-quality John Deere parts – from filters to belts, blades to batteries, we’ve got you covered. Choose speedy delivery or pickup options at your local dealer.
Additional Resources
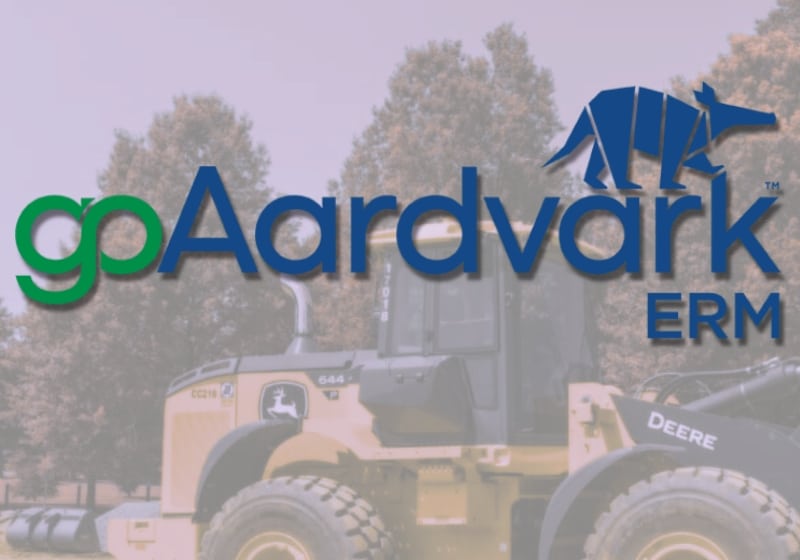
Aardvark provides predictive maintenance and remote monitoring solutions designed specifically for heavy construction equipment. This resource can help you and your team proactively address equipment issues, reduce downtime, and keep machines running efficiently.